La construction des autoroutes en climat continental présente quelques particularités : les épaisseurs de chaussées sont fortes du fait d’une nécessaire protection contre les effets du gel, et les matériaux bitumineux sont formulés pour avoir des propriétés mécaniques équilibrées entre résistance à l’orniérage et résistance à la fissuration. Cet article est consacré à la construction d’une section de l’autoroute M30 en Hongrie, dont la chaussée mixte est composée d’une couche de fondation en grave traitée aux liants hydrauliques et de couches de base, de liaison et de roulement en enrobés.
Le fond de cohésion mis en place par la Communauté européenne en 1994 permet d’accélérer le développement économique des pays éligibles, les infrastructures routières étant un maillon fondamental de l’essor économique.
La Hongrie a ainsi considérablement étendu son réseau autoroutier et le dernier plan de développement prévoit l’achèvement des liaisons vers les pays limitrophes en 2025.
Depuis plus de 15 ans, Colas Hongrie a acquis un savoir-faire dans les grands travaux de construction routière avec à ce jour plusieurs dizaines de références autoroutières. En décembre 2017, Colas Hungaria et Colas Ut (Colas Hongrie) ont été déclarés adjudicataires pour concevoir et construire la section B de l’autoroute M30 entre Miskolc et Tornyosnemeti, un maillon essentiel de la Via Carpatia qui, depuis la Hongrie, va desservir l’Est de la Slovaquie, notamment la ville de Kosice, puis la Pologne et la mer Baltique (figure 1).
La longueur de la section neuve est de 24,2 km et comprend, outre la construction de la section courante, l’aménagement des routes existantes, la construction d’un centre de maintenance complexe ainsi qu’un centre de gestion autoroutier, deux échangeurs et un itinéraire cyclable.
Les principales quantités de matériaux se décomposent en : 345 000 t d’enrobés, 300 000 t de grave ciment, 900 000 t de couche de forme et 2,6 millions de m3 de terrassement. Colas Hongrie et ses filiales spécialisées ont construit la totalité des 21 ouvrages d’art incluant le forage de 10 000 mètres de pieux et l’installation de 13 400 mètres de poutres de précontraintes préfabriquées.
Les travaux de réalisation de la couche de forme ont été terminés avant l’hiver et les premières tonnes de matériaux de chaussées ont été validées sur des sections tests. L’ouverture de la section est prévue en juillet 2021.
figure_1_viacarpatia.jpg
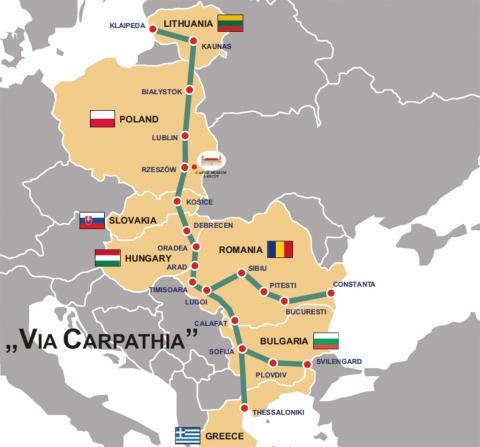
DESCRIPTION DES STRUCTURES DE CHAUSSÉES
En Hongrie, les structures de chaussées autoroutières sont calculées pour une durée de vie de 30 ans. Elles font appel à des matériaux de hautes performances et conjuguent souvent les effets de protection au gel, apportés par les couches de fondation traitées aux liants hydrauliques et la souplesse et la facilité de maintenance des couches bitumineuses (base, liaison et roulement).
Il est à noter que, pour renforcer la durée de vie et les caractéristiques de résistance à l’orniérage, les matériaux bitumineux font appel à des bitumes modifiés par des polymères de température bille et anneau minimale de 65 °C.
Il est à noter que, pour renforcer la durée de vie et les caractéristiques de résistance à l’orniérage, les matériaux bitumineux font appel à des bitumes modifiés par des polymères de température bille et anneau minimale de 65 °C.
La structure type en section courante (figure 2) se compose de :
- 4 cm de couche de roulement en Stone Mastic Asphalt (SMA), mélange granulats et mastic, SMA11 ;
- 9 cm de couche de liaison en béton bitumineux AC22 ;
- 10 cm de couche de base en béton bitumineux AC22 ;
- 20 cm de couche de fondation en matériaux traités aux liants hydrauliques (MTLH) ;
- 20 cm de couche de forme.
Les parties supérieures des terrassements, à base de matériaux locaux stabilisés par de la chaux, présentent une portance minimale de 65 MPa.
figure_3_profilen_travers.jpg
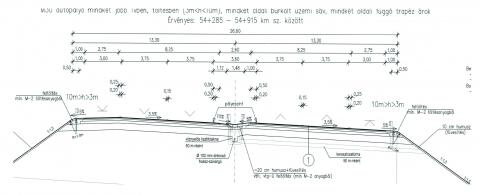
CARACTÉRISTIQUES DES MATÉRIAUX
Matériaux traités aux liants hydrauliques
Le ciment utilisé est un CEMIII/A 32.5 R-MS, dosé à 4,9 % (soit 105 kg/m3), qui a permis d’obtenir des résistances en compression comprises entre 3 et 4 MPa sur la grave-ciment de granularité 0/32 mm (figures 3 et 4).
figure_4.jpg
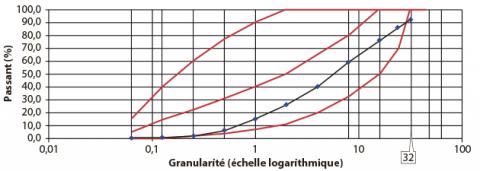
figure_5.jpg
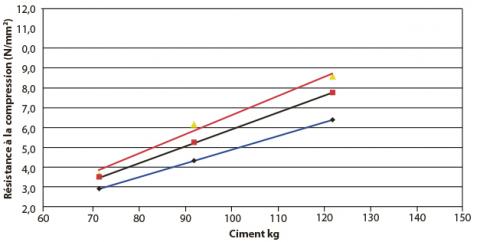
Béton bitumineux
Parmi les trois couches de chaussées en enrobés, c’est la présentation de la formulation de la couche de fondation de type AC22 qui a été retenue pour cet article.
Sa courbe granulométrique figure dans le tableau 1. La validation de l’étude de formulation du mélange bitumineux de granularité 22 mm comprend, pour le marché hongrois :
- la satisfaction du respect des seuils de composition, comme la courbe granulométrique ou la teneur en liant ;
- des valeurs de performances mécaniques, comme le module ou la fatigue.
Elle est résumée dans le tableau 2.
tableau_1.jpg

tableau_2.jpg
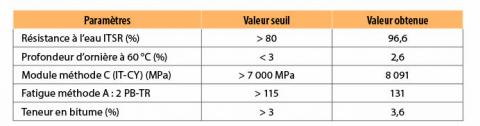
MISE EN ŒUVRE DES MATÉRIAUX DE CHAUSSÉES
Matériaux traités aux liants hydrauliques
La couche de fondation en grave-ciment est mise en œuvre au-dessus de la couche de forme de 20 cm. Le mélange traité au ciment doit être livré sur le site de façon à assurer sa mise en place avant le début de prise du ciment, ce qui nécessite le bâchage des camions afin d’éviter la perte d’humidité du mélange. Chaque jour, des échantillons sont prélevés afin de vérifier la qualité de la livraison.
En fonction des conditions météorologiques, en particulier par temps sec ou ensoleillé, le support doit être arrosé pour éviter le dessèchement rapide de la grave-ciment, qui est mise en œuvre à des températures comprises entre 5 et 30 °C.
La production ne démarre qu’après réalisation de sections d’essai et approbation par le superviseur des travaux.
La mise en œuvre se déroule en deux passes en utilisant 2 finisseurs, décalés d’une trentaine de mètres, l’un pour la section courante, l’autre pour les bandes d’arrêt d’urgence.
Une attention particulière a été accordée au positionnement du joint longitudinal qui ne doit pas se superposer au futur joint des enrobés mis en œuvre par la suite. Les joints longitudinaux sont donc espacés de 10 à 20 cm.
L’excellence opérationnelle est le fil rouge de l’ensemble des phases de mise en œuvre :
- Au démarrage des travaux, la table du finisseur est placée sur des cales dédiées à l’épaisseur de mise en œuvre de la couche de chaussée.
- Les joints de reprise sont proprement sciés avant la reprise des travaux.
- Les matériaux sont déchargés des camions en continu de manière à éviter tout arrêt de l’atelier de mise en œuvre.
- Au moment de l’alimentation du finisseur par les semi-remorques, les chocs sont évités avant le démarrage de la mise en œuvre.
- L’épaisseur d’application est ajustée de façon à obtenir l’épaisseur requise après compactage.
- La vitesse du finisseur est de 1 à 3 mètres par minute.
La tolérance sur l’épaisseur est de 1 cm ; elle est contrôlée en continu tous les 100 mètres.
La compacité doit être de 95 % de la valeur de l’étude.
Une préfissuration de la grave-ciment est ensuite assurée afin de contrôler l’espacement des fissures de retrait de la couche traitée.
Enfin, l’application d’une couche de cure, à base d’une émulsion cationique de bitume dosée autour de 600 g/m2, permettra de maintenir une hygrométrie optimale dans le matériau traité.
Le matériel utilisé lors de ce chantier comprend 4 finisseurs et 4 compacteurs, dont 3 à bande lisse et 1 à pneumatiques.
Enrobés bitumineux
Les enrobés bitumineux sont fabriqués dans une centrale fixe neuve discontinue de 240 t/h (photo 1) située à l’extrémité sud du chantier, à 19 km de distance et 25 à 30 minutes de temps de transport. Le chantier est relié en continu par téléphone avec la centrale pour la bonne qualité de la pose. Les enrobés sont transportés par camions bâchés dont la benne est protégée par un produit anticollage.
photo_1.jpg
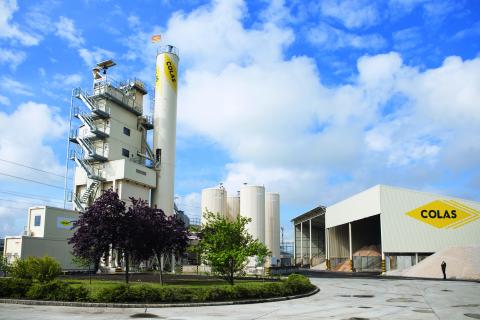
La mise en œuvre des enrobés est classique (photo 2), sauf problème de planéité particulier, et le contrôle consiste à vérifier leur épaisseur et leur pente transversale.
photo_2.jpg
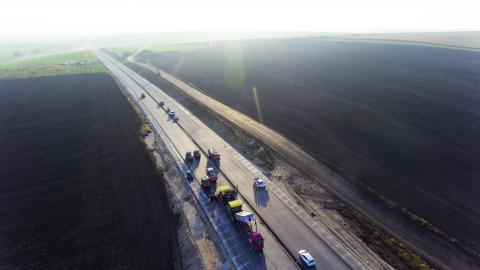
Le marquage des bords de la grave-ciment doit permettre de suivre parfaitement l’alignement des couches appliquées. À partir de 3 camions arrivés sur le site, la mise en œuvre peut commencer.
La vitesse du finisseur, habituellement de 3 à 4 m/min, peut être ajustée en fonction de la livraison des enrobés, de manière à assurer une mise en œuvre continue des couches. Le compactage respecte, à partir de la partie de plus basse altimétrie de la section transversale, le principe de recouvrement des passes prévu dans le plan de répandage.
Le recouvrement des joints selon une procédure spécifique permet d’effacer toute trace de celui-ci. Les joints de reprise sont découpés et enduits d’émulsion de manière appropriée.
La température des enrobés est contrôlée sur le site avant chaque livraison ; elle doit se situer entre 160 et 180 °C pour les bitumes modifiés de grade dur.
Après mise en œuvre, la température des enrobés au niveau des vis du finisseur doit dépasser 140 °C, sauf cas particulier de bitumes modifiés au polymère et produits d’entreprise approuvés.
Les moyens matériels se composent notamment de 2 finisseurs et 4 compacteurs.
SUIVI ET CONTRÔLE QUALITÉ
Pour ce type de projet, le client, l’agence de développement des infrastructures NIF Zrt, demande :
- un contrôle permanent de toutes les phases de travaux ;
- une validation et un enregistrement de toutes les études ;
- un compte rendu quotidien des travaux d’exécution réalisés.
Cela nécessite donc d’importants moyens à la fois sur le site pour réaliser tous les essais demandés, mais aussi du côté du service de contrôle de la qualité qui gère l’ensemble des documentations mises à la disposition du client.
Ainsi, comme pour toute phase de travaux, l’approbation par l’ingénieur représentant du client d’un plan d’échantillonnage, de mesures et d’essais conditionne le démarrage du chantier. De ce fait, 19 personnes du département de technologie de Colas Hongrie travaillent sur ce projet :
- 2 administrateurs, ingénieurs de ce projet, sont chargés de piloter le suivi technique.
- 6 personnes sont affectées au contrôle de la qualité : 3 pour la construction des structures, 3 pour la construction des routes ;
- 1 superviseur sur chantier coordonne et planifie le travail du laboratoire.
- Il est entouré de 5 assistants de laboratoire qui travaillent in situ sur la section courante de l’autoroute comme sur les voies rétablies et aménagées : 2 assistants contrôlent la conformité des enrobés livrés sur le chantier ; 2 assistants testent les livraisons de béton pour les ouvrages ainsi que celles de la grave traitée aux liants hydrauliques pour la couche de fondation de chaussée ; 1 technicien fait les analyses de sol pour le terrassement.
La quantité d’essais réalisés est donc très importante : en 2019, plus de 7 000 rapports de laboratoire ont été produits.
CONCLUSION
La construction du réseau autoroutier hongrois est presque achevée et couvrira bientôt la totalité du pays. Le maillon de l’autoroute M30, qui relie la région de Miskolc à la Slovaquie voisine, est un tronçon de haute technicité, qui voit l’intervention de nombreux acteurs locaux et auquel Colas Hongrie participe activement.
Les structures de chaussées semi-rigides présentées sont adaptées aux contraintes météorologiques du climat continental et conçues pour une longue durée de vie.
Afin de garantir un haut niveau de qualité, de bon augure pour la fin de la construction de cette section, les caractéristiques de performance des matériaux utilisés sont très élevées ; l’organisation et les moyens de suivi et de contrôle sont très importants.